|
|
Screen Printing & Dyeing Equipment |
|
|
The Steamer / Polymerizer |
|
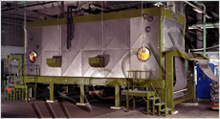 |
For the continuous fixation of all classes of Dyes on all known Fabrics, by passing the Fabric in Loop Form through Steam, or through Thermal Oil Heated Air/Steam Re-circulating system, at Atmospheric Pressure.
Operator’s inspection/viewing points, through amply sized HT ‘Unbrako’ glassware, enabling operator greater vision and thus control of the fabric whilst passing through the steam chamber. |
|
|
SQUEEZE MANGLES (Nips) : |
|
2 Bowl Transporter/Squeeze Mangles (Nips), Each Squeeze Mangle (Nip) comprising of a pair of heavy duty rigidly stayed fabricated Steel uprights having been formatted to support the following:- |
|
THE STEAMER / POLYMERIZER: |
|
The Printed Fabric is guided with minimum tension through the Machine Entry system into the Steam Chamber and formed into hanging Loops of programmed length over Loop Carrier Rollers by a Loop Formation Frame.
The Loop Carrier Rollers, which are retained within a pair of endless Transport Chains, and are covered with Insulating material to prevent moisture formation and slippage of the Fabric, move the Fabric Loops through the Steam Chamber.
At every step of the endless Transport Chains movement, the Loop Rollers rotate via a Rack & Pinion system, to continually advance the Fabric on the Loop Rollers, thus ensuring the Fabric uniformity of conditioning by allowing the total Fabric to pass through all the exact same Steaming Conditions within the Steam Chamber.
The Machine Pre-set Running Speed, will automatically control the Duration Time of the Fabric passing within the Steam Chamber, which is then continuously being delivered to the Fabric Plaiter section via the Exit Roller arrangement at the rear section of the Steam Chamber. |
|
CONTROL PANEL |
|
Comprising of a "Free Standing" cubicle, housing all of the necessary Switch-gear and related Electrical Instrumentation required for Operating the Steamer/Polymerizer Unit.
The controlling parameters of the Machine having been simplified and/or automated to enable the Operator to simply Set the Controls to obtain Repeatability and constant monitoring. |
|
ENTRY & DELIVERY ARRANGEMENTS |
|
The Standard Steamer/Polymerizers are supplied with Frontal Entry and a Rear Plaiter Delivery arrangement.
For Operational conveniences, a Combined Frontal Entry & Delivery arrangement can be supplied on request, however it is advisable to note that these Combined Frontal Entry & Delivery are more suitable for Woven Fabrics, due to increase in the Fabric tension. |
|
STEAM AGEING AT LOW TEMPERATURE |
|
The Temperature and Humidity Factors on the Machine are simply achieved via a Steam Flow Input Control System, equally delivering a selected Pre-set amount of Steam to boil a selected Pre-set level of Water contained within each Panel Section forming the Steam Chamber Walls.
The use of this method, creates a controllable uniform Steam Vapour at 102o Cent., which maintains the Steam Chamber Uniformity of Temperature.
The Steam Chamber Humidity Factor, (constantly being monitored by a Humidity Metering system), is simply controlled by the Operator by minutely adjusting the amount of Water contained within the Steam Chamber Walls via the Water Level Control Unit, to suit the required Humidity Level (after which the Water Level can then be Re-set for Repeatability).
The use of this method of Boiling the Water inside the Walls of the Steam Chamber Panels, allows the Input Steam which boils the water to Condense back into water again, therefore using the Input Steam to Generate the required Humidity Level without the need for External non-purified water. |
|
HIGH TEMPERATURE POLYMERIZING IN
HOT AIR/STEAM
THERMAL-OIL HEATING SYSTEM FOR HIGH TEMPERATURE |
|
The Air/Steam medium is heated through a series of Thermal Oil Heat Exchangers, which are suitably located within the Polymerizing Chamber to maximize the Temperature equilibrium, and is then delivered through the Ducting system via a series of purposely designed Circulating Fans to ensure the even distribution of the medium within the Polymerizing Chamber.
The incorporated Temperature Control system, automatically adjusts the Thermal Oil flow to the Heat Exchangers to the Pre-set desired Temperature necessary for the Fabric being treated (Maximum 190o Cent.).
A Steam Exhaust system, suitably located at the lower section of the Steam Chamber, automatically removes the excess Spent/Contaminated Air/Steam medium. |
|
|